(一)调查酒损的情况
啤酒总损失率是指啤酒生产过程中,各工序在报告期内所发生的流失量与总量之比。是冷却损失率、发酵损失率、过滤损失率、包装损失率的总和。
为了弄清楚酒损的真实状况,调查小组重点作了四项工作:
第一,对清酒桶液位计作了检查,清洗及更换工作,以保证清酒计童的准确性。
第二,重新标定了糖化二组两口煮沸锅容量及沉淀槽容量,为避免争议,特邀请车间和财务科派代表参加,使用新标尺共同测定麦汁产量。
第三,对车间及计划科的酒损统计工作进行调查了解。
第四,对二、三车间生产过程中的啤酒损失作了查定工作。测定的数据详见表2-6.表2-7.表2-8:
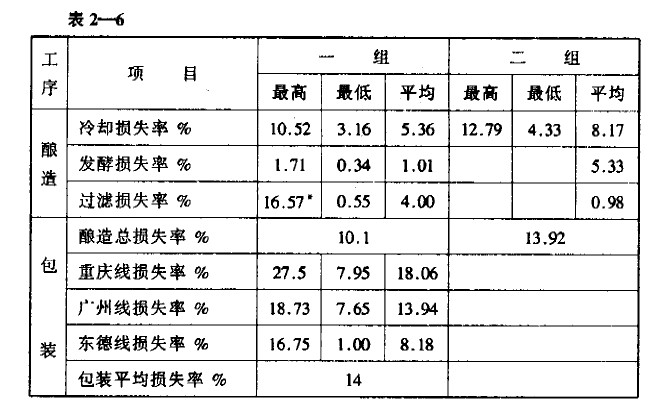
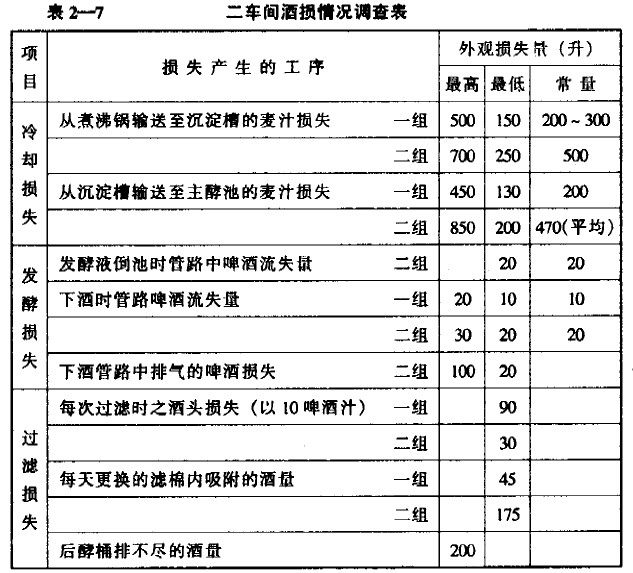
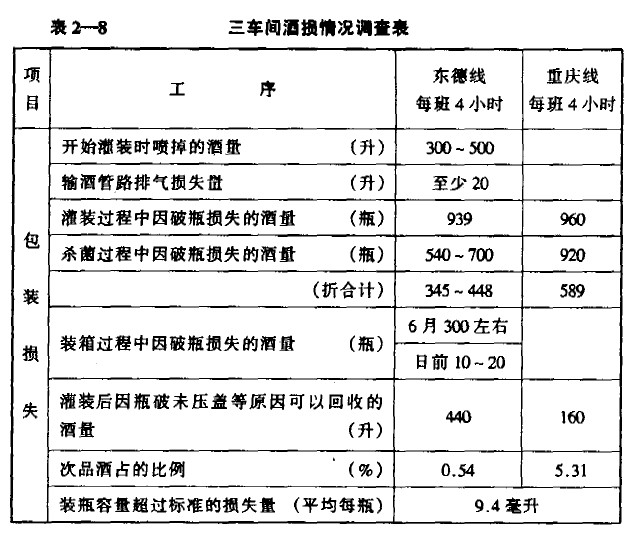
说明表中几个数据的情况:
I.测定一组酿造工序过滤损失率最高的数据16.57%,为6月27日一组过滤的损失度,后酵桶号41,液童8.75千升,滤后清酒桶号4号,清酒量7.3千升。
2.测定二组平均发酵损失率5.33%时,由于主酵液量及后酵计量不准,此数据仅供参考。
3,测定二级平均过滤损失率0.98%时,因后酵桶液量计量不准,此数据仅供参考。从原始记录看,多数批量的后酵液过滤后,一点损失也没有,但实际损失远高于此。
表2-6、表2-7、表2-8所调查的酒损数据,较真实地反映了啤酒生产过程中的酒损状况,从总损失率指标看,已落后于本企业过去的水平。请看调查组收集的总损失率统计数据。
一季度该厂总损失率为27.5%,远远落后于全国平均水平和先进水平。全国四十六家大、中型啤酒厂的啤酒总损失率平均为14.05%,广州啤酒厂仅为5.53%,为全国先进水平,共总损失率5.53%是在啤酒生产过程中不可避免损失的范围内。详见表2-10。
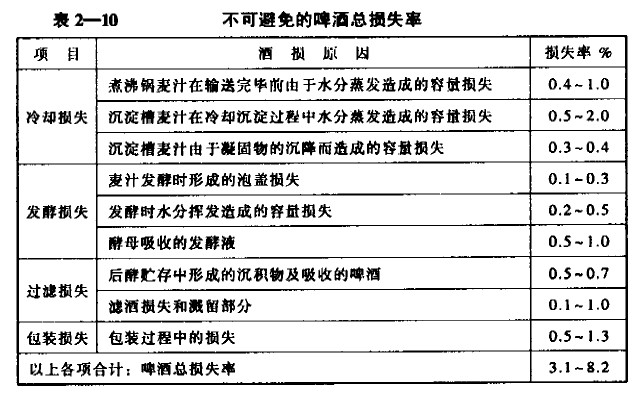
表2-10统计的不可避免的啤酒总损失率是在3.1%一8.2%之间。纵横相比,明显地看出了差距和落后,该厂的酒损比全国平均水平高1倍,比全国先进水平高4倍。如此惊人的浪费,必然会导致啤酒产量减少、成本增加、利润降低。为了进一步用具体的数据说明问题,调查组的同志收集了大最的信息资料,以本厂的财务成本决算和生产统计报表的有关数据为准,推算出“酒损与产量、成本、利润关系计算表”。
(二)酒损与产盆、成本、利润关系分析
对于啤酒厂,酒损指标的高低,直接影响企业的利润。酒损与产A、成本、利润的关系,实质上是投人与产出的关系。在投人相同数童原材料和劳动童的情况下,如果酒损高就意味着产!低、成本高、效益差。如果酒损低,则产A高、成本低、效益好。下面所列出的计算式,说明了它们之间的相关关系。
P=S一Y
S=WX Y=C1+C2
C=F+CvX C2=Cv'X
P=WX一(F+CvX+Cv'X)
式中符号说明:
P:啤酒销售利润
S:啤酒销售收人
Y:啤酒总成本
w:每吨啤酒的平均销售价格
x:啤酒的产销量
C1:啤酒的生产总成本
F:固定费用
Cv:单位产品的变动费用
C2:啤酒的销售成本
Cv':单位产品的销售税、销售费用和教育附加费
固定费用包括车间经费、企业管理费和职工福利基金。变动费用由原材料、燃料动力和工资构成。产品产量包括以白龙潭啤酒为主产品的7个啤酒品种产量。
根据1-6月的实际资料计算,F=1583475.51元二158.35万元:Cv二310.75元/吨;Cv'=197.61元/吨;w=781.65元/吨;啤酒投料量是10581吨;饮料亏损及营业外支出39.84万元。需要特别说明一点,即计算由于降低酒损所增产啤酒的变动费用时,不能按公式简单地用Cv乘以x,因为啤酒在酿造和包装生产过程中,每个环节都可能产生酒损,各个环节的酒损造成的变动费用比例不等,例如:酿造第一道工序发生酒损造成的变动费用损失最小,只计烤麦芽和酒花的费用144.64元/吨,占单位产品变动费用的46.55% (144.64/310.75),而包装后一道工序发生酒损造成的变动费用损失最大,占变动费用的100%,所以,计算由于降低酒损增加啤酒产量的变动费用,不能直接用增加量乘以变动费用,而要用增加量乘以30%的单位产品变动费用(30%x310.75)。
咨询组的同志将各项指标的实际数据代人公式,清楚地展现出昆明啤酒厂酒损与产量、成本、利润之间的相互关系,从这一关系中,给予人们许多启迪,详见表2-11所示:
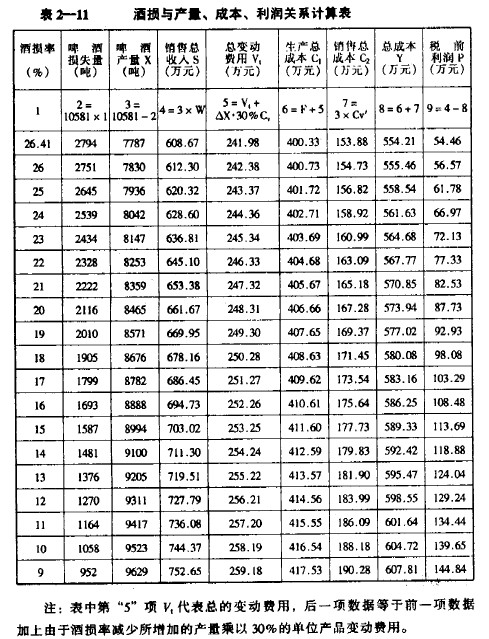
表2-11所计算的数字,是假设酒损率每下降一个百分点,而市场平均售价、固定费用、单位产品变动费用、单位产品的销售税、销售费用和教育附加费等不变的情况下,所引起的啤酒产量、 销售收人、成本、利润等指标的变化。该厂1一6月份的酒损率为26.41%,啤酒损失量达2794吨,啤酒产量为7787吨,每吨啤酒的成本是711.71元,税前利润54.46万元。若加强管理,能使酒损率降至本企业曾达到的较好水平13%,那么,在不增加任何投入的情况下,可增产啤酒1418吨,增长18.2%;每吨啤酒的成本为646.9元,下降9.1%;税前利润124.04万元,增长1.28倍;假如再加把劲,使酒损率降到国家二级企业标准的9%,则可增产啤酒1842吨,增长23.65%;每吨啤酒成本为631.23元,下降11.3%;税前利润144.84万元,增长1.66倍。,
(三)造成酒损率增高的缘由
咨询组全体同志通过细致调查、认真分析。一致认为形成酒损率超标的主要原因是缺乏科学、严格的管理。表现为以下几点:
第一,忽视对酒损指标的管理,没有建立科学、合理的检查、计算、考核制度。
酒损率是一项直接影响企业经济效益的重要指标,理应列为内部管理的重点。但是,遗憾的是厂领导班子并不重视这项工作。没有把酒损率纳人考核范围。酒损指标的高低与科室、车间、班组没有任何关系。虽然影响企业的经济效益,但是丝毫不波及个人收人,酒损率再高也无所谓,大家都不关心。即便是填写在统计报表上的数据,,一也是不符合事实的天文数字。因为计量不准,原始记录不全,没有按规定分别计算出冷却、发酵、过滤、包装损失率,最后再得出总损失率。据调查:按厂里的车间分工,冷却、发酵、过滤三道工序属二车间,包装工序由三车间完成。而计算各工序损失率时,却人为地将四道工序分成两段计算,违反规定地进行测算。一段是算冷却损失率,另一段是把发酵、过滤、包装三道工序合并一起的混合损失率,这一指标跨越了两个车间。最后得出的总损失率对实际工作没有实际指导意义。指标的变化不能说明什么地方出问题。如此关键的指标被忽略实属企业内部管理的一大失误。
第二,操作不规范,致使每道工序均产生本来完全可以避免的酒损。
1.冷却
首先由煮沸锅至沉淀槽的热麦汁损失,操作人员漫不经心,测出外观平均损失童高达507升。其次由沉淀槽至前酵池的麦汁损失,因放人下水道和麦汁溢出池子等原因,两组测定的总损失量为500升。
2.发酵
倒池时从管道中的流失量平均每次20升;下酒过程中,每下一池后酵管中残留部分损失量20一30升;倒池时,由于主酵池容纳不下,溢出损失无法测定,某次酒液溢出达1分钟之久;下酒管路排气,操作不当,只图流速快,大盘排气,可造成酒损倍增,多达100升左右;下酒结束,后酵桶已满,操作工不在现场,致使酒液从桶口溢出……
3。过滤
操作不当,重复过滤使酒损增加;更换的滤棉内所含啤酒没有回收.每天测定两组的啤酒损失达120升;棉饼过滤的酒头没有回收,每天二组共损失啤酒至少为110升;更换清酒管路时,管道内残留的酒没有回收而流失,也造成损失。
4。包装
灌装过程中,由于责任心不强、技术不熟练,没有控制好灌装压力温度而喷酒冒沫造成损失;
东德线灌装机在排除管路中气体时,从接取排出的酒量分析,每次开始灌装时,至少损失20升酒。另外,在开始灌装时,约30箱酒都因喷酒冒沫灌不满而重新灌装,喷掉的酒至少288升;
操作不当,灌装阀液位没有按规定标准控制好,使装瓶容量超标,据一次抽样50瓶测定,平均每瓶超量9.4毫升,增加包装损失1.47%;
灌装过程中的破瓶残酒从不回收;
滤出的酒液,操作工人没有经过8小时的稳定时间,即刻灌装则引起喷酒,以造成不必要的损失。
杀菌也造成极大损失,测定东德线杀菌机,每班破瓶500一700瓶,损失酒量320一450升。如果用新瓶,破损量高达1000瓶,损失酒640升;
装箱损失也很大,六月份测定东德线装箱机,每班损失多达300瓶;
由于各道工序没有严格把关,最终必然出现大量次品,损失惨重。
第三,设备因素。
灌装机装酒阀不密封造成灌装损失;
某些发酵池底面不平或坡度不够,使酒液无法排空。例如:后酵一组10号桶因地基沉降,估计约有200升酒液不能排出;
麦汁泵、酒泵漏损也是原因之一。
第四,控制不严。
后酵液澄清不良,反复过滤必然使酒损增加;
冷却麦汁输送人前酵池时,经常发生容纳不了而从池边滋流的情况。此外,有的主酵池比前酵池容t小得多,当倒池将完时,又发生容纳不了而使发酵液流失的现象,损失量相当大。
第五,生产计划科统计各项酒损指标没有反映出实际状况。
造成酒损统计数据与实际出人较大的原因有三点:
一是计童工具不准确,每200升标定容量,实际只有197一199升。
二是由于计里不准和没有严格按《啤酒工业生产专业统计计算方法》中规定统计的数据代人公式计算。
三是计算酒损失率的方法不符合要求。
(四)改善方案
第一,建立酒损分析制度,保证对酒损指标的管理落在实处。
制度明确规定:
第一条:厂部成立酒损分析领导小组;
第二条:酒损分析领导小组的主要职能是:定期召开检查酒损指标的例会;针对存在的问题提出办法和措施;对降低酒损做出成绩的人员,提出表彰和奖励,对失职者进行批评和惩罚;酒损分析会批准的数据是进行生产统计、财务成本、经济核算、计发奖金的依据之一。凡属会议决定的事项,有关车间和部门必须认真贯彻执行。
第三条:有关科室(车间)的职责。
生产计划科。负责收集汇总酒损的有关基础数据,编制酒损分析月报;健全和管理好全厂的原始记录和统计报表;会同财务科、技术科拟定和下达对车间的酒损定额指标。
技术科。负责对酒损分析会提出措施的实施情况进行检查;制定和完善工艺操作规程并督促其严格执行;负责衡器、计量容量、计量标尺的检验、修理和测定工作;
检验科。按工艺和质量管理要求,按时提交化验单;及时对产成品和在制品进行质量检查、验收和签发产品合格证。
财务科。进行经济活动分析,促进酒损的降低;协同生产计划科,完善原始记录管理,制定酒损定额指标。
劳动人事科。按工艺要求合理安排劳动定员;将酒损指标纳入经济承包责任制的考核内容.与职工的经济利益挂钩;组织开展以降低酒损为主要内容的岗位技术练兵活动,并作为考工晋级的依据之一。
供销科。严格空瓶验收,向车间及时供应合格的空瓶;加强成品验收和管理,人库要及时登记上帐,做到帐、物相符;产品每月清库盘点一次,销售损失不得超过定额。
车间。严格执行工艺操作规程,管好用好设备,落实降低酒损的各项措施,不断降低啤酒损耗,认真填写原始记录,按时提出统计表。二、三车间要有明确的清酒交接手续和记录。
第四条:酒损的统计和计算,按《啤酒工业生产专业统计计算方法》中的有关规定和公式进行。
第二,改进设备和操作,有效地降低酒损率。
安装及定期清洗液位计,保证计A正确;
采取水顶麦汁和蒸气或压缩空气两种方法,将管道内麦汁顶人沉淀槽,以减少糖化麦汁由煮沸锅打至沉淀槽的损失;
在过滤槽上方增设一个至少有350升容蟹的盛贮器,减少沉淀槽至前酵池的麦汁损失;
改进二组前酵工序的下酒管路,减少排气损失;
控制装瓶容量,加强空瓶检验;
定期对各种设备进行检查、维修、保养;
要求每位操作人员均要严格按操作规程工作。
第三,改进工艺,减少酒损。
杜绝麦汁或发醉液,酒液滥出现象;从发芽、塘化、发酵工艺进行改进,避免重复过滤。
第四,重新标定设备容量,准确计量。
第五,健全计量统计工作。
每道工序必须认真做好原始记录,正确如实计量本工序的产量;
按照要求统计所需要的各项数据,数据要真实、可靠、准确;
正确计算酒损指标;
当计算各品种之综合冷却损失率时,140麦汁产量应换算成100热麦汁产童后再与其他浓度之热麦汁产量相加。
换算公式:

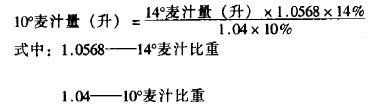
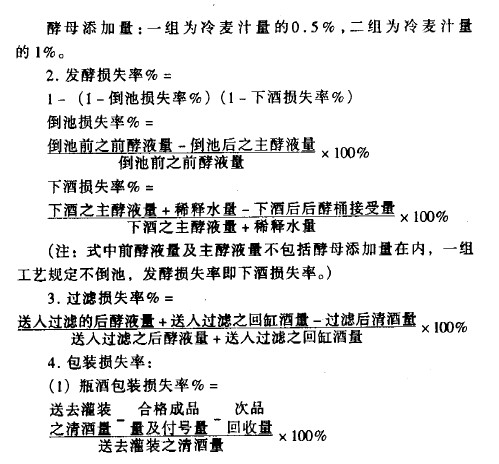
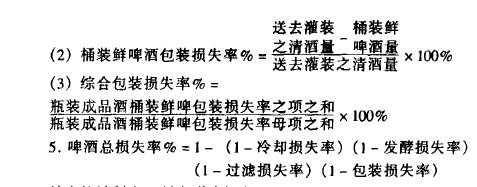
健全统计制度。制度明确规定:
I.每个工序必须认真填写产量日报表,一式两份,每天报至车间统计员处,待统计员汇总后再报至计划科;
2.职责明确。二车间统计员负责计算一组、二组的冷却损失率、发挥损失率、过滤损失率及各项对应的综合损失率。,三车间统计员负责计算东德线包装损失率、广州线包装损失率、重庆线包装损失率及各项对应的综合损失率,还有鲜啤包装损失率、瓶酒鲜啤包装综合损失率。
每月都要上报计划科,便于检查和监控。
3,计划科负责计算各种浓度的冷却损失率、发酵损失率、过滤损失率及包装损失率。啤酒总损失率及各项对应的综合损失率。将计算结果与车间报来的各项综合损失率进行比较,两个数值应相等,若不相等,需要仔细检查,直到相等为止。
(五)实施改善方案,取得显著成效
通过上述改善方案的实施,酒糟率指标下降了10%, 10月份达16.37%,取得可喜的绩效。